Liquefied natural gas

Liquefied natural gas or LNG is natural gas (consisting primarily of methane, CH4) that has been converted into liquid form for ease of transport and storage. More simply put, it is the liquid form of the natural gas that people use in their homes for cooking and for heating,
A typical raw natural gas contains only about 80% methane and a number of higher boiling hydrocarbons as well as a number of impurities. Before it is liquefied, it is typically purified so as to remove the higher-boiling hydrocarbons and the impurities. The resultant liquefied natural gas contains about 95% or more methane and it is a clear, colorless and essentially odorless liquid which is neither corrosive nor toxic.[1][2]
LNG occupies only a very small fraction (1/600th) of the volume of natural gas and is therefore more economical to transport across large distances. It can also be stored in large quantities that would be impractical for storage as a gas.[1][2]
Liquefaction plants for the production of LNG
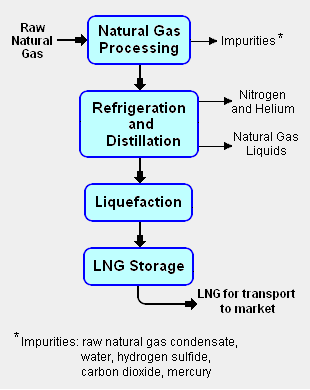
Fig.1: Block flow diagram of the LNG liquefaction process. See Natural gas processing for more details.
The liquefaction process involves separating the raw natural gas from any associated water and high-boiling hydrocarbon liquids (referred to as natural gas condensate) that may be associated with the raw gas. The raw gas is then further purified in a natural gas processing plant to remove impurities such as the acid gases hydrogen sulphide (H2S) and carbon dioxide (CO2), any residual water liquid or vapor, mercury, nitrogen, and helium which could cause difficulty downstream. (See the block flow diagram of the liquefaction process in Fig.1)
The purified natural gas is next refrigerated and distilled in a train of fractionators, first a demethanizer column to recover the purified natural gas (predominantly methane) and then in a deethanizer, a depropanizer and a debutanizer to separate and recover ethane (C2H6), propane (C3H8), butanes (C4H10) and any higher boiling hydrocarbons, collectively referred to as natural gas liquids (NGL). The natural gas is then condensed into a liquid at essentially atmospheric pressure by using further refrigeration to cool it to approximately −162 °C (−260 °F).
There are a number of refrigeration systems available for liquefying natural gas. The global LNG industry has adopted two main liquefaction processes:
- the propane pre-cooled multi-component refrigeration (C3/MR) process, also known as the APCI process and used by the majority (about 80%) of LNG plants[3]
- the pure refrigerant cascade process
The first LNG plants in Algeria and Alaska (see history section below) were based on the cascade process using propane, ethylene, and methane as refrigerants. Since then, however, the majority of large LNG projects have been based on the C3/MR process. Various studies have shown that the efficiencies of the two main processes are similar.[3][4][5]
As mentioned above, the reduction in volume makes LNG much more cost efficient to transport over long distances where pipelines do not exist. Where transporting natural gas by pipelines is not possible or economical, it can be transported by specially designed cryogenic sea-going vessels called LNG carriers or by either cryogenic rail or road tankers.
History
Natural gas liquefaction dates back to the 1820s when British physicist Michael Faraday experimented with liquefying different types of gases. German engineer Carl Von Linde built the first practical vapor-compression refrigeration system in the 1870s.
The first commercial LNG liquefaction plant was built in Cleveland, Ohio, in 1941 and the LNG was stored in tanks at atmospheric pressure, which raised the possibility that LNG could be transported in sea-going vessels. In January 1959, the world's first LNG carrier, a converted freighter named The Methane Pioneer, containing five small, insulated aluminium tanks transported 5,000 m3 (about 2,250 metric tons[6]) of LNG from Lake Charles, Louisiana in the United States of America to Canvey Island in England's Thames river. That voyage demonstrated that LNG could be transported safely across the oceans. During the next 14 months, that same freighter delivered seven additional cargoes with only a few small problems.[2][7]
The demonstrated ability to transport LNG in sea-going vessels spurred the building of large-scale LNG liquefaction plants at major natural gas fields world-wide. The first large-scale LNG plant began operating in 1964 at Arzew, Algeria and initially produced about 2,560 metric tons/day (t/day[6]) of LNG. In 1969, another LNG plant began operating near Kenai, Alaska and initially produced LNG at a rate of about 3,400 t/day.[2][8]
By mid-2008, there were 19 LNG liquefaction plants operating in 15 countries worldwide, and the three largest were:
- Bontang project in Indonesia, producing about 64,000 t/day
- Ras Gas project in Qatar, producing about 59,000 t/day
- Arzew project in Algeria, producing about 49,000 t/day
There were also 65 LNG receiving terminals (often referred to regasification terminals) operating in 19 countries world-wide.[8]
LNG transportation
As of 2008, a typical sea-going LNG carrier could transport about 150,000 m3 (70,000 t) of LNG, which will become about 92,000,000 standard cubic metres[9] of natural gas when regasified in a receiving terminal. LNG carriers are similar in size to an aircraft carrier and are very expensive to build and to operate. Therefore, they cannot afford to have idle time. They travel fast, at an average speed of 18 to 20 knots, as compared to 14 knots for a sea-going crude oil carrier. Also, loading at the LNG liquefaction plants and unloading at the receiving terminals usually requires only 15 hours as an average.
All LNG carriers have a double-hulled structure specially designed to prevent leakage or rupture in case of an accident. The cargo (LNG) is stored at atmospheric pressure and -162 ºC in specially insulated tanks (referred to as the "containment structure") inside the inner hull. The cargo containment structure consists of a primary liquid tank, a layer of insulation, a secondary liquid barrier, and a secondary layer of insulation. Should there be any damage to the primary liquid tank, the purpose of the secondary barrier is to prevent leakage. All surfaces in contact with LNG are constructed of materials resistant to the extreme low temperature. Therefore, the material is typically stainless steel or aluminium or a nickel-iron alloy known as "invar".
About 57% of the worldwide LNG carrier fleet uses tanks, which are supported by and conform to the shape of carrier's hull, to contain the LNG cargo. Such carriers are commonly referred to as "membrane type" vessels. The other major type of LNG carrier, constituting about 41% of the worldwide fleet, uses self-supported spherical tanks to contain the LNG, with the upper half of the spheres being above-deck as can be seen in Fig.2. Such carriers are commonly referred to as "Moss type" vessels (named after the Norwegian company, Moss Maritime).
Most LNG vessels use steam-turbines to provide propulsion power and those vessels use the gas that boils off from the cargo as fuel for generating steam. Therefore, LNG carriers do not arrive at the destination port with the same LNG quantities as were loaded at the liquefaction plant. The accepted maximum figure for boil-off is about 0.15% of cargo volume a day. Thus, for a 20 day voyage, the LNG cargo will have been reduced by about 3%. Recent advances in technology allow the installation of plants on-board the vessels that can re-liquefy the boil-off, which is then returned to the cargo tanks. Because of this, the builders and users of LNG carriers can now consider the use of more efficient diesel engines rather than steam-turbines.
As of mid-2008, there were 247 LNG carriers in the worldwide fleet and the total capacity of the fleet was 30,800,000 cubic metres of LNG.[8]
LNG receiving terminals
LNG receiving terminals (often referred to as regasification terminals) receive LNG carriers, unload their LNG cargoes and store the LNG in tanks. When required, the LNG is withdrawn from the storage tanks, converted back into natural gas by using heat exchangers to vaporize the LNG, and then sent to the end consumers via a local pipeline grid.
The main components of a receiving terminal are the LNG carrier unloading berths and port facilities, LNG storage tanks, vaporizers to convert the LNG into its original gaseous form, and a pipeline link to the local natural gas grid. LNG tankers may also be unloaded offshore, away from congested and shallow ports. This is accomplished using a floating mooring system and unloading the carriers via an undersea insulated LNG pipeline to the land-based regasification facility.[4]
The major component of the receiving terminal is the vaporization equipment which heats the LNG from –161.5°C to more than 5°C in order to convert the LNG back into its gaseous phase. Conceptually, vaporizers are relatively simple units in which LNG is typically pumped through heat exchangers where it is heated by exchanging heat with a warmer fluid in a heat exchanger. The warmer fluid may be sea water, warm water or other warm fluid. There are also a number of other methods for vaporizing the LNG.[10]
In conventional receiving terminals facilities either onshore or offshore, the unloaded LNG is stored onshore in large tanks until gas is required by the end consumers.
LNG storage tanks
Large LNG storage tanks are cylindrical and have a low aspect ratio (i.e.,height to width ratio). They are typically constructed with a post-tensioned concrete outer wall and a high-nickel steel inner wall, with insulation between the inner and outer walls.[11] The tanks have domed roofs made of steel or concrete. The storage pressure in such tanks is quite low, less than 10 kPa (0.10 atm). Sometimes underground or partially underground tanks are used for storage.
Smaller cylindrical LNG storage tanks, about 1,000 m3 (264,000 gallons) or less, are usually vacuum-jacketed, pressure vessels. The storage pressure in such tanks may range from less than 50 kPa (0.50 atm) to over 1,000 kPa (10 atm) and they may be either horizontal or vertical.
LNG safety aspects
In its liquid state, LNG is neither flammable nor explosive. For LNG to burn, it must first vaporize, mix with air in the proper proportions (the flammable range is 5 to 15 volume %[12]), and then be ignited.[1][13][14]
When LNG is released into the ambient atmosphere because of a leak, spill or any other cause (on land or at sea), it immediately begins to vaporize by absorbing heat from the ground or the sea water. At the usual ambient air temperature of about 15 to 40 °C, natural gas is much lighter than air. However, the natural gas vapor formed when LNG vaporizes is very cold (i.e., −160 °C) and therefore much denser than the ambient air, which means that the initial vapor will remain at ground or sea level. The vapor will begin mixing with air and water moisture in the air will be condensed to form a visible vapor cloud. As the cloud is initially formed, it contains too much natural gas to be flammable. It will linger near ground level until further heat is absorbed and the natural gas rises and mixes with more air. As that occurs, the concentration of natural gas within the cloud will begin to decrease. At some point, the natural gas concentration in the cloud will decrease to where the gas is in the flammable range and becomes ignitable. If an ignition source is present at that point, only that part of the cloud which is within the flammable range will burn. The vapor cloud will not explode unless it is confined. Any part of the cloud that enters a building or becomes confined in a congested area will become explosive if it encounters an ignition source.[15][16]
There are possible hazards associated with LNG other than fire or explosions:[2][15]
- Rapid Phase Transition: The sudden vaporization or phase transition from liquid to vapor that has occurred upon occasion when LNG has been spilled into water has caused a physical explosion. No injuries have occurred from an RPT of LNG but equipment has been damaged. The explosive overpressures caused by RPTs have not been well measured as yet, but indications are that the overpressures have not been high enough to cause personnel injury.
- Asphyxiation: For human death to occur from asphyxiation, the LNG vapors must reduce the normal oxygen concentration in the air (about 21 volume %) to less than 6 volume %. This would occur when the concentration of LNG vapors in the air is about 71 volume %. Breathing is impaired when the oxygen level in the air is reduced to less than 15 volume % and vomiting occurs when the oxygen level is below 10 volume %, which correspond to the concentration of LNG vapors in the air being about 28 and 52 volume %respectively.
- Freeze burns: A single incident in which a person experienced a freezer burn by being sprayed with an LNG leak in 1977 when a valve ruptured during the loading of an LNG carrier.
- Roll over in storage tanks: Due to the pressure exerted by the hydraulic head of LNG in a tank, the lower level of LNG in the tank is at a pressure and equilibrium temperature somewhat higher than the LNG at the upper level in the tank and, hence, is somewhat less dense than the LNG at the upper level. Thus, the tank contents are susceptible to the lower level suddenly rising to the top level because of the density difference. This is referred to as "roll over". Should this occur, a small fraction of the LNG would immediately vaporize into gas because it was no longer subjected to any hydraulic head pressure. Since the expansion ratio of LNG vapor to liquid is about 600 to 1, even a small amount of vaporization can generate a large volume of gas. The resulting sudden increase in tank pressure can exceed the capacity of the pressure relief valves and perhaps lead to a failure of the roof or wall of the tank. The first such roll over occurred in 1971 and slightly damaged the LNG tank roof. This problem is mitigated by monitoring the tank temperatures at various levels and by providing pumped mixing systems.
Overall, the LNG industry has an excellent safety record compared to other hydrocarbon processing plants. As of late 2003, there were 23 LNG liquefaction plants worldwide, 58 receiving (regasification) terminals, and 224 sea-going LNG carriers, altogether handling approximately 168 million metric tons of LNG every year. LNG had been safely delivered across the oceans for over 40 years. In that time there had been over 45,000 LNG carrier voyages, covering more than 100,000,0000 miles (160,900, 000 km) without major accidents or safety problems either in port or on the high seas. The LNG industry has had to meet stringent standards set by countries such as the United States of America, Japan, Australia, and European nations.[2][14][17]
According to the U.S. Department of Energy, over the life of the industry, eight marine incidents worldwide have resulted in spillage of LNG, with some hulls damaged due to cold fracture, but no cargo fires have occurred. Seven incidents not involving spillage were recorded, two from carrier groundings, but with no significant cargo loss; that is, repairs were quickly made and leaks were avoided. There have been no LNG shipboard fatalities.[14]
Isolated accidents with fatalities occurred at several onshore facilities in the early years of the industry. More stringent operational and safety regulations have since been implemented.[14] A fairly complete listing and discussion of the incidents that occurred with sea-going carriers, at land-based facilities (liquefaction plants and receiving terminals) and with on-road LNG tankers is available online.[17]
Units and conversions
Most of the available LNG technical literature uses certain dimensional units and conversions that vary from one literature source to another. The key units and conversions are set forth below so as to make available a single set of self-consistent data:
Basic units:
- 1 cubic metre (m3) = 35.315 cubic feet (ft3)
- 1 metric ton (t) = 1 tonne = 1,000 kg = 2,204.6 pound = 1.1023 short ton (ton) (a)
- 1 short ton (ton) = 2,000 pound = 0.9072 metric ton (t) = 0.9072 tonne = 907.2 kg
Definitions:
- LNG density = 450 kg/m3 = 0.45 t/m3 (b)
- 1 metric ton of LNG = 2.222 m3 of LNG = 1,360 m3 of natural gas (at an assumed pressure of 1 atm and a temperature of 0 °C) (b) (c)
- 1 short ton of LNG = 71.18 ft3 of LNG = 46,053 ft3 of natural gas (at an assumed pressure of 1 atm and a temperature of 60 °F) (b) (c)
Notes:
(a) The U.S. customary units include both a short ton (2,000 pound) and a long ton (2,240 pound).
(b) The LNG density varies from one literature source to another. The volumes of natural gas per metric ton of LNG and per short ton of LNG also vary from one source to another since each source presumably uses different reference conditions of gas temperature and pressure.
(c) The LNG technical literature, for the most part, does not explicitly define the reference conditions of gas temperature and pressure when stating natural gas volumes in
either cubic metres or cubic feet.
LPG, a somewhat similar substance
Liquefied petroleum gas or LPG is a somewhat similar substance consisting of either propane or butane or mixtures of propane and butane with possibly some traces of propylene and butylenes. Those compounds are by-product gases recovered in petroleum refineries and from natural gas processing plants. They have much higher boiling point temperatures than LNG and are easily liquefied at about 20 °C and pressures ranging from 2 atmospheres (for pure butane) to 8 atmospheres (for pure propane).
LPG is also referred to as LP gas or, in some countries, as autogas. It is widely sold in pressurized steel cylinders such as shown in Fig.2 as well as in much smaller cylinders. LPG has many uses, including:
- fuel for residential heating and cooking in rural areas where natural gas is not available
- fuel for barbecue grills, heating and cooking in motor homes, and camping cookers.
- a refrigerant for small air-conditioners
- fuel for small soldering and welding torches
- fuel for automobiles designed to use LPG (see Fig. 7)
References
- ↑ 1.0 1.1 1.2 Frequently Asked Questions About LNG From the website of the California Energy Commission
- ↑ 2.0 2.1 2.2 2.3 2.4 2.5 Introduction To LNG Michelle Michot Foss (updated January 2007), Center for Energy Economics (CEE), Bureau of Economic Geology, Jackson School of Geosciences, University of Texas
- ↑ 3.0 3.1 The World of Energy : LNG Technology - Processes, Liquefaction Processes Fundamentals
- ↑ 4.0 4.1 Liquefied Natural Gas Chain
- ↑ LNG Technology S. Madhavan (August 2010), Kellogg Brown & Root, Inc., Houston, Texas
- ↑ 6.0 6.1 Note: 1 metric ton = 1 t = 1 tonne = 1,000 kg = 2,204.6 pounds = 1.1023 short tons
- ↑ Michael R. Tusiani and Gordon Shearer (2007). LNG: A Nontechnical Guide. Pennwell Corp., p.138. ISBN 0-87814-885-X.
- ↑ 8.0 8.1 8.2 Fostering LNG Trade: Role of the Energy Charter 2008, Appendices A , C and E, from the website of the Energy Charter Secretariat.
- ↑ Note: Presumably , a standard cubic metre of gas is defined as gas at reference conditions of 1 atmosphere pressure and a temperature of 0 °C. However, most of the LNG technical literature does not explicitly define the reference conditions.
- ↑ Study focuses on six LNG regasification systems Brian Eisentrout, Steve Wintercorn and Barbara Weber, LNG Journal, July/August 2006, page 21.
- ↑ Emaco Group: Case Studies
- ↑ Note: If there is less than 5 volume % or more than 15 volume % of natural gas vapor in the air, the gas will not burn.
- ↑ Frequently Asked Questions: LNG] From the website of the Federal Energy Regulatory Commission
- ↑ 14.0 14.1 14.2 14.3 LNG Safety and Security Michelle Michot Foss (October 2003), Center for Energy Economics (CEE), Bureau of Economic Geology, Jackson School of Geosciences, University of Texas
- ↑ 15.0 15.1 John M. Woodward and Robin Pitblado (2010). LNG Risk Based Safety: Modeling and Consequence Analysis. John Wiley and American Institute of Chemical Engineers. ISBN 0-470-31764-7.
- ↑ Report On Issues Regarding The Existing New York Liquefied Natural Gas Moratorium 1998, from the website of the New York State Energy and Research Development Authority (NYSERDA). The report concluded that safety concerns associated with LNG terminal facilities were adequately addressed by existing Federal, State and local statutes and regulations. For those reasons, the study recommended: that the New York State Legislature discontinue the existing moratorium.
- ↑ 17.0 17.1 History of International LNG Operations, March 2009