User:Milton Beychok/Sandbox: Difference between revisions
imported>Milton Beychok |
imported>Milton Beychok |
||
Line 57: | Line 57: | ||
LNG receiving terminals (often referred to as regasification terminals) receive LNG carriers, unload their LNG cargoes and store the LNG in tanks. When required, the LNG is withdrawn from the storage tanks, converted back into natural gas by using [[heat exchanger]]s to vaporize the LNG, and then sent to the end users via a local pipeline grid. | LNG receiving terminals (often referred to as regasification terminals) receive LNG carriers, unload their LNG cargoes and store the LNG in tanks. When required, the LNG is withdrawn from the storage tanks, converted back into natural gas by using [[heat exchanger]]s to vaporize the LNG, and then sent to the end users via a local pipeline grid. | ||
The main components of a receiving terminal are the LNG carrier unloading berths and port facilities, LNG storage tanks, vaporizers to convert the LNG into its original gaseous form, and a pipeline link to the local natural gas grid. LNG tankers may also be unloaded offshore, away from congested and shallow ports. This is accomplished using a floating mooring system and unloading the carriers via an undersea insulated LNG pipeline to the land-based regasification facility. | The main components of a receiving terminal are the LNG carrier unloading berths and port facilities, LNG storage tanks, vaporizers to convert the LNG into its original gaseous form, and a pipeline link to the local natural gas grid. LNG tankers may also be unloaded offshore, away from congested and shallow ports. This is accomplished using a floating mooring system and unloading the carriers via an undersea insulated LNG pipeline to the land-based regasification facility.<ref name=natgas/> | ||
The major component of the receiving terminal is the vaporization equipment which heat the LNG from –161.5°C to more than 5°C in order to convert the LNG back into its gaseous phase. Conceptually, vaporizers are relatively simple units in which LNG is typically pumped through heat exchangers where it is heated by exchanging heat with a warmer fluid in a [[heat exchanger]]. The warmer fluid may be sea water, warm water or other warm fluid. There are also a number of other methods for vaporizing the LNG.<ref>[http://www.cbi.com/images/uploads/technical_articles/LNGjournaljulAug06.pdf Study focuses on six LNG regasification systems]] Brian Eisentrout, Steve Wintercorn and Barbara Weber, ''LNG Journal'', July/August 2006, page 21.</ref> | The major component of the receiving terminal is the vaporization equipment which heat the LNG from –161.5°C to more than 5°C in order to convert the LNG back into its gaseous phase. Conceptually, vaporizers are relatively simple units in which LNG is typically pumped through heat exchangers where it is heated by exchanging heat with a warmer fluid in a [[heat exchanger]]. The warmer fluid may be sea water, warm water or other warm fluid. There are also a number of other methods for vaporizing the LNG.<ref>[http://www.cbi.com/images/uploads/technical_articles/LNGjournaljulAug06.pdf Study focuses on six LNG regasification systems]] Brian Eisentrout, Steve Wintercorn and Barbara Weber, ''LNG Journal'', July/August 2006, page 21.</ref> |
Revision as of 18:44, 21 February 2011
Liquefied natural gas or LNG is natural gas (predominantly methane, CH4) that has been converted into liquid form for ease of transport and storage. More simply put, it is the liquid form of the natural gas that people use in their homes for cooking and for heating,
A typical raw natural gas contains only about 80% methane and a number of higher boiling hydrocarbons as well as a number of impurities. Before it is liquefied, it is typically purified so as to remove the higher-boiling hydrocarbons and the impurities. The resultant liquefied natural gas contains about 95% or more methane and it is a clear, colorless and essentially odorless liquid which is neither corrosive nor toxic.[1][2]
LNG occupies only a very small fraction (1/600th) of the volume of natural gas and is therefore more economical to transport across large distances. It can also be stored in large quantities that would be impractical for storage as a gas.[1][2]
Liquefaction plants for the production of LNG
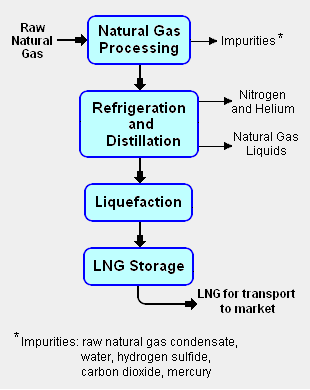
Fig.1: Block flow diagram of the LNG liquefaction process. See Natural gas processing for more details.
The liquefaction process involves separating the raw natural gas from any associated water and high-boiling hydrocarbon liquids (referred to as natural gas condensate) that may be associated with the raw gas. The raw gas is then further purified in a natural gas processing plant to remove remove impurities such as the acid gases hydrogen sulfide (H2S) and carbon dioxide (CO2), any residual water liquid or vapor, mercury, nitrogen and helium which could cause difficulty downstream. ( See the block flow diagram of the liquefaction process in Fig.1)
The purified natural gas is next refrigerated and distilled to recover ethane (C2H6), propane (C3H8), butanes (C4H10) and any higher boiling hydrocarbons, collectively referred to as natural gas liquids (NGL). The natural gas is then condensed into a liquid at essentially atmospheric pressure by using further refrigeration to cool it to approximately -162 °C (260 °F).
There are a number refrigeration systems available for liquefying natural gas. The global LNG industry has adopted two main liquefaction processes:
- the propane pre-cooled multi-component refrigeration (C3/MR) process, also known as the APCI process and used by the majority of LNG plants
- the pure refrigerant cascade process
The first LNG plants in Algeria and Alaska (see history section below) were based on the cascade process using propane, ethylene, and methane as refrigerants. Since then, however, the majority of large LNG projects have been based on the C3/MR process. Various studies have shown that the efficiency of the two main processes is similar.[3][4][5]
As mentioned above, the reduction in volume makes LNG much more cost efficient to transport over long distances where pipelines do not exist. Where transporting natural gas by pipelines is not possible or economical, it can be transported by specially designed cryogenic sea-going vessels called LNG carriers or by either cryogenic rail or road tankers.
History
Natural gas liquefaction dates back to the 1820s when British physicist Michael Faraday experimented with liquefying different types of gases. German engineer Carl Von Linde built the first practical vapor-compression refrigeration system in the 1870s.
The first commercial LNG liquefaction plant was built in Cleveland, Ohio, in 1941 and the LNG was stored in tanks at atmospheric pressure, which raised the possibility that LNG could be transported in sea-going vessels. In January 1959, the world's first LNG carrier, a converted freighter named The Methane Pioneer, containing five small, insulated aluminum tanks transported 5,000 m3 (about 2,250 metric tons[6]) of LNG from Lake Charles, Louisiana in the United States to Canvey Island in England's Thames river. That voyage demonstrated that LNG could be transported safely across the oceans. During the next 14 months, that same freighter delivered seven additional cargoes with only a few small problems.[2][7]
The demonstrated ability to transport LNG in sea-going vessels spurred the building of large-scale LNG liquefaction plants at major gas fields world-wide. The first large-scale LNG plant began operating in 1964 at Arzew, Algeria and initially produced about 2,560 metric tons/day (MT/day[6]) of LNG. In 1969, another LNG plant began operating near Kenai, Alaska and initially produced LNG at a rate of about 3,400 MT/day.[2][8]
By mid-2008, there were 19 LNG liquefaction plants operating in 15 countries worldwide, and the three largest were:
- Bontang project in Indonesia, producing about 64,000 MT/day
- Ras Gas project in Qatar, producing about 59,000 MT/day
- Arzew project in Algeria, producing about 49,000 MT/Day
There were also 65 LNG receiving terminals (often referred to regasification terminals) operating in 19 countries world-wide.[8]
LNG transportation
As of 2008, a typical sea-going LNG carrier could transport about 150,000 m3 (70,000 MT) of LNG, which will become about 92,000,000 standard metres[9] natural gas when regasified in a receiving terminal. LNG carriers are similar in its size to an aircraft carrier and are very expensive to build and to operate. Therefore, they cannot afford to have idle time. They travel fast, at an average speed of 18 to 20 knots[10], as compared to 14 knots for a sea-going crude oil carrier. Also, loading at the LNG liquefaction plants and unloading at the receiving terminals usually requires only 15 hours as an average.
All LNG carriers have a double-hulled structure specially designed to prevent leakage or rupture in case of an accident. The cargo (LNG) is stored at atmospheric pressure and -162 ºC in specially insulated tanks (referred to as the "containment structure") inside the inner hull. The cargo containment structure consists of a primary liquid tank, a layer of insulation, a secondary liquid barrier, and a secondary layer of insulation. Should there be any damage to the primary liquid tank, the purpose of the secondary barrier is to prevent leakage. All surfaces in contact with LNG are constructed of materials resistant to the extreme low temperature. Therefore, the material is typically stainless steel or aluminum or a nickel-iron alloy known as "invar".
About 57% of the worldwide LNG carrier fleet uses tanks, which are supported by and conform to the shape of carrier's hull, to contain the LNG cargo. Such carriers are commonly referred to as "membrane type" vessels. The other major type of LNG carrier, constituting about 41% of the worldwide fleet, uses self-supported spherical tanks to contain the LNG, with the upper half of the spheres being above-deck as can be seen in Fig.2. Such carriers are commonly referred to as "Moss type" vessels (named after the Norwegian company, Moss Maritime).
Most LNG vessels use steam-turbines to provide propulsion power and those vessels use the gas that boils off from the cargo as fuel for generating steam. Therefore, LNG carriers do not arrive at the destination port with the same LNG quantities as were loaded at the liquefaction plant. The accepted maximum figure for boil-off is about 0.15% of cargo volume a day . Thus, for a 20 day voyage, the LNG cargo will have been reduced by about 3%. Recent advances in technology allow the installation of plants on-board the vessels that can re-liquefy the boil-off, which is then returned to the cargo tanks. Because of this, the builders and users of LNG carriers can now consider the use of more efficient diesel engines rather than steam-turbines.
As of mid-2008, there were 247 LNG carriers in the worldwide fleet and the total capacity of the fleet was 30,800,000 cubic metres of LNG.[8]
LNG receiving terminals
LNG receiving terminals (often referred to as regasification terminals) receive LNG carriers, unload their LNG cargoes and store the LNG in tanks. When required, the LNG is withdrawn from the storage tanks, converted back into natural gas by using heat exchangers to vaporize the LNG, and then sent to the end users via a local pipeline grid.
The main components of a receiving terminal are the LNG carrier unloading berths and port facilities, LNG storage tanks, vaporizers to convert the LNG into its original gaseous form, and a pipeline link to the local natural gas grid. LNG tankers may also be unloaded offshore, away from congested and shallow ports. This is accomplished using a floating mooring system and unloading the carriers via an undersea insulated LNG pipeline to the land-based regasification facility.[3]
The major component of the receiving terminal is the vaporization equipment which heat the LNG from –161.5°C to more than 5°C in order to convert the LNG back into its gaseous phase. Conceptually, vaporizers are relatively simple units in which LNG is typically pumped through heat exchangers where it is heated by exchanging heat with a warmer fluid in a heat exchanger. The warmer fluid may be sea water, warm water or other warm fluid. There are also a number of other methods for vaporizing the LNG.[11]
Contact with seawater in warmer climates or heated water in colder climates keeps the heat exchangers warm.
In conventional onshore-based regas facilities, offloaded LNG is stored in large tanks, either above ground or semi-buried, until gas is required by consumers. Semi-buried tanks, which can be spaced closely together, are most common in Japan, where land is scarce. LNG is also being offloaded offshore, usually by modified LNG tankers that also have regasification units on board. These ships have the ability to discharge gaseous methane directly into a pipeline grid or discharge LNG by offshore moorings into cryogenic pipelines for gasification onshore, as well as conventional LNG offloading to a shore facility by fixed arms. Ship-to-ship LNG transfer is still in its early stages and all the technical hurdles have yet to be fully ironed out. Once this process will become conventional, we could see large ships discharging to smaller ships offshore, and these smaller ships will be able to come directly to port, convert the LNG to methane which will be directly piped to the local grid.
Some Statistics
Units and conversions
Most of the available LNG technical literature uses certain dimensional units and conversions that need to be defined and clarified. The key units and conversions are set forth below:
Basic units:
- 1 cubic metre (m3) = 35.315 cubic feet (ft3)
- 1 metric ton (MT) = 1 tonne = 1,000 kg = 2,204.6 pound = 1.1023 short ton (ton)(a)
- 1 short ton (ton) = 2,000 pound = 0.9072 metric ton (MT) = 0.9072 tonne = 907.2 kg
Definitions:
- LNG density = 450 kg/m3 = 0.45 MT/m3
- 1 MT of LNG = 2.222 m3 of LNG = 1,360 m3 of natural gas (at an assumed pressure of 1 atmosphere and a temperature of 0 °C)(b)
- 1 ton of LNG = 71.18 ft3 of LNG = 46,053 ft3 of natural gas (at an assumed pressure of 1 atmosphere and a temperature of 60 °F)(b)
Notes:
(a) The U.S. customary units include both short ton (1,000 pound) and long ton (2,240 pound).
(b) The LNG technical literature, for the most part, does not explicitly define the reference conditions of gas temperature and pressure when stating natural gas volumes in either cubic metres or cubic feet.
References
- ↑ 1.0 1.1 Frequently Asked Questions About LNG From the website of the California Energy Commission
- ↑ 2.0 2.1 2.2 2.3 Introduction To LNG Michelle Michot Foss (January 2007), Center for Energy Economics (CEE), Bureau of Economic Geology, Jackson School of Geosciences, University of Texas
- ↑ 3.0 3.1 Liquefied Natural Gas Chain
- ↑ The World of Energy : LNG Technology - Processes, Liquefaction Processes Fundamentals
- ↑ LNG Technology S. Madhavan (August 2010), Kellogg Brown & Root, Inc., Houston, Texas
- ↑ 6.0 6.1 Note: 1 metric ton = 1 MT = 1 tonne = 1,000 kg = 2,204.6 pounds = 1.1023 short tons
- ↑ Michael R. Tusiani and Gordon Shearer (2007). LNG: A Nontechnical Guide, p.138. ISBN 0-87814-885-X.
- ↑ 8.0 8.1 8.2 Fostering LNG Trade: Role of the Energy Charter 2008, Appendices A , C and E, from the website of the Energy Charter Secretariat.
- ↑ Note: Presumably , a standard cubic metre of gas is defined as gas at reference conditions of 1 atmosphere pressure and a temperature of 0 °C. However, most of the LNG technical literature does not explicitly define the reference conditions.
- ↑ Note: 1 knot = 1 nautical mile/hour = 1.852 km/hour = 1.15 statute mile/hour = 6,076 feet/hour
- ↑ Study focuses on six LNG regasification systems] Brian Eisentrout, Steve Wintercorn and Barbara Weber, LNG Journal, July/August 2006, page 21.